Tool design
We utilize both Solidworks and Mastercam for Solidworks packages in our injection and blow mold tool design. This enables us to quickly build and visualize parts, and then to design the tool around the part.
Fabrication
Tooling is designed and manufactured in house, giving us speed and flexibility that our customers really appreciate. Our customers speak directly with our engineers and tooling manager, from the design phase right through to the completed part.
Ability to make changes and modifications quickly
Because we manufacture our tooling in house, should any modifications be needed during part qualification, we are able to respond very quickly.
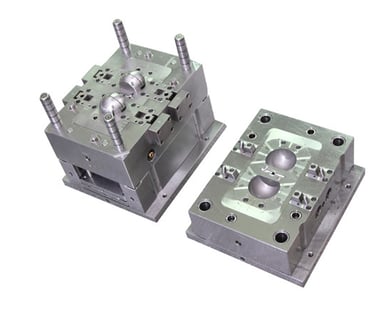
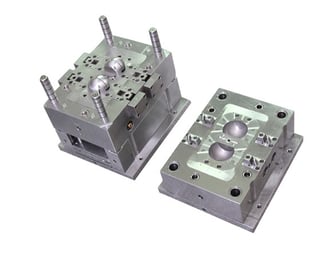
TOOLING CAPABILITIES
Injection Molding
Injection molding press sizes
Our Injection molding presses range in size from 110 to 500 tons, allowing us to mold from under a gram to over 2kg
Molded parts size
We have the capability to design and mold parts from a few mm up to 30cm long and 50cm in diameter.
Automation
We have installed automated work cells on several of our presses, improving repeatability and increasing throughput capabilities.
Reducing environmental contamination
Contamination control is a priority at Filterwise and several of our ultra clean injection molding presses have ISO Class 7 enclosures around the feed hopper and tool area. HEPA enclosures also protect parts from airborne contamination as they exit the work cell.
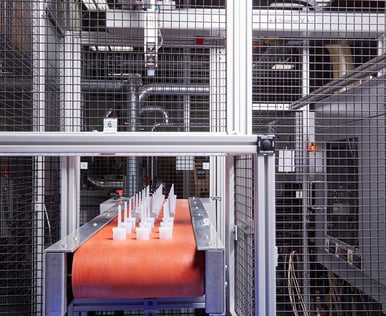
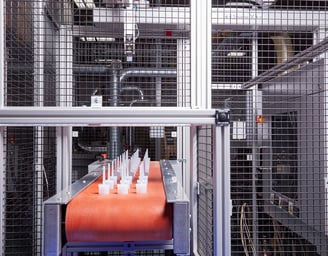
MOLDING CAPABILITIES
Assembly and Post-Cleaning
A wide range of assembly operations, from very simple to very complex, is available. For some semiconductor customer we perform acid cleaning to remove ultratrace contamination through assembly operations.
ISO Class 7 Cleanroom Assembly
In addition to our blow molding cleanroom we have a large ISO Class 7 clean room for assembly and can also offer sterilization of parts to accepted GMP standards.
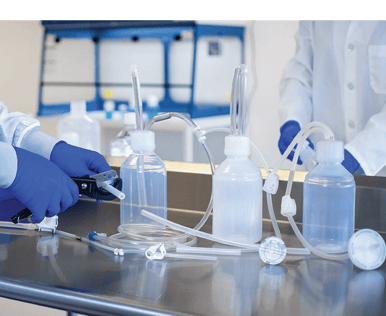
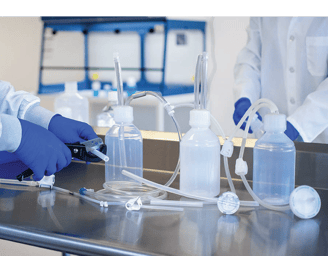
SECONDARY OPERATIONS
Take the functionality and uniqueness of your custom parts even further with Filterwise laser engraving capabilities. Our in-house engraving unit works by delivering high levels of energy to the surface of your product, thus vaporizing the material into fumes to engrave deep, permanent markings. The laser utilizes an air-cooled source, which helps keep the process simple while delivering consistent power for more reliable and accurate results.
Compared to stamping and other laser marking techniques, laser engraving is faster, more durable, and imparts less stress on the part. It also provides advantages specific to fluoropolymers – causing no impact on their chemical and temperature-resistant properties and standing as the only technique that can produce reliable results for ultra-clean resins. This is a significant benefit for those engaged in cryopreservation, acid washing, and similar sensitive use cases.
Filterwise laser engraving is a great value-add for a variety of applications in the life sciences, manufacturing, and semiconductor industries, including:
Logos – Add your branding to any custom part
Date Codes – Know precisely when your part was manufactured
Use Matrices – Keep track of number of uses without needing stickers or other markings
Unique Identifiers – Graduation marks, product names, and much more
Save time and the need for additional vendors with our one-stop laser engraving service.
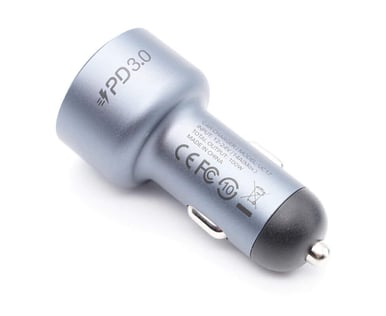
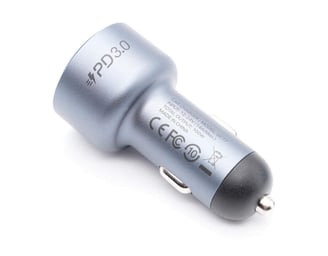
LASER ENGRAVING
Product testing
Our engineering lab has a wide array of capabilities including leak testing and pressure decay testing, to ensure that all parts we design meet specifications under extreme conditions.
Dimensional Inspection
Our extensive range of metrology equipment allows us to inspect parts for dimensional accuracy, both during part qualification and ongoing quality assurance.
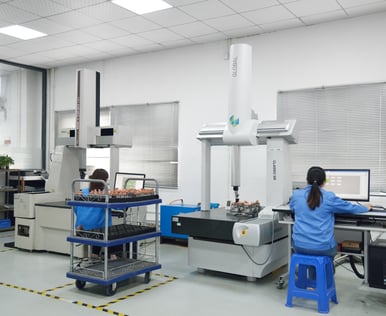
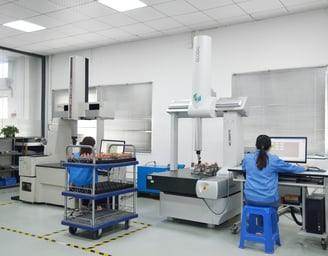
QUALIFICATION
Filterwise
Innovative solutions for safe water filtration.
Sustainability
Quality
contact@filterwise.com
© 2024. All rights reserved.
ABOUT